For decades, the rail industry has been battling a complex and costly problem. In parts of the country’s vast track network, there are spots where the lines deteriorate rapidly – sometimes as often as every six weeks. Constantly fixing them is a drain on time and resources, resulting in higher carbon emissions and also increasing safety risks with engineers having to be on the track so regularly. But now, thanks to research by academics at the University of Southampton, these weak points can be spotted early and the problem solved, potentially saving the rail industry millions of pounds in repairs.
Researcher Dr David Milne was first funded by Network Rail almost a decade ago as a PhD student to carry out research into using sensors to improve rail maintenance, and that groundbreaking work continues today. His first project involved embedding sensors at spots along lines that needed regular maintenance visits to monitor movement in the track.
David says: “I worked very closely with a project engineer to design and employ a set of equipment that monitored the track movements to take measurements they wouldn’t normally get. They used that technique at different problem sites to understand what was going on and give them the confidence to try more innovative approaches to maintenance.”
The sensors collected constant data about the track that could be analysed then used to draw up better maintenance plans.
Measuring performance makes it possible to target maintenance accurately, which is much more cost effective and saves a huge amount of carbon.
Three forms of modern rail maintenance methods were then tested out in these hotspots. These included placing rubber pads under the sleeper, lowering the sleeper into the ballast and packing extra ballast material around the rail and sleeper. All three methods were found to improve the longevity of stretches of track, but adding extra material was found to be the most effective approach.
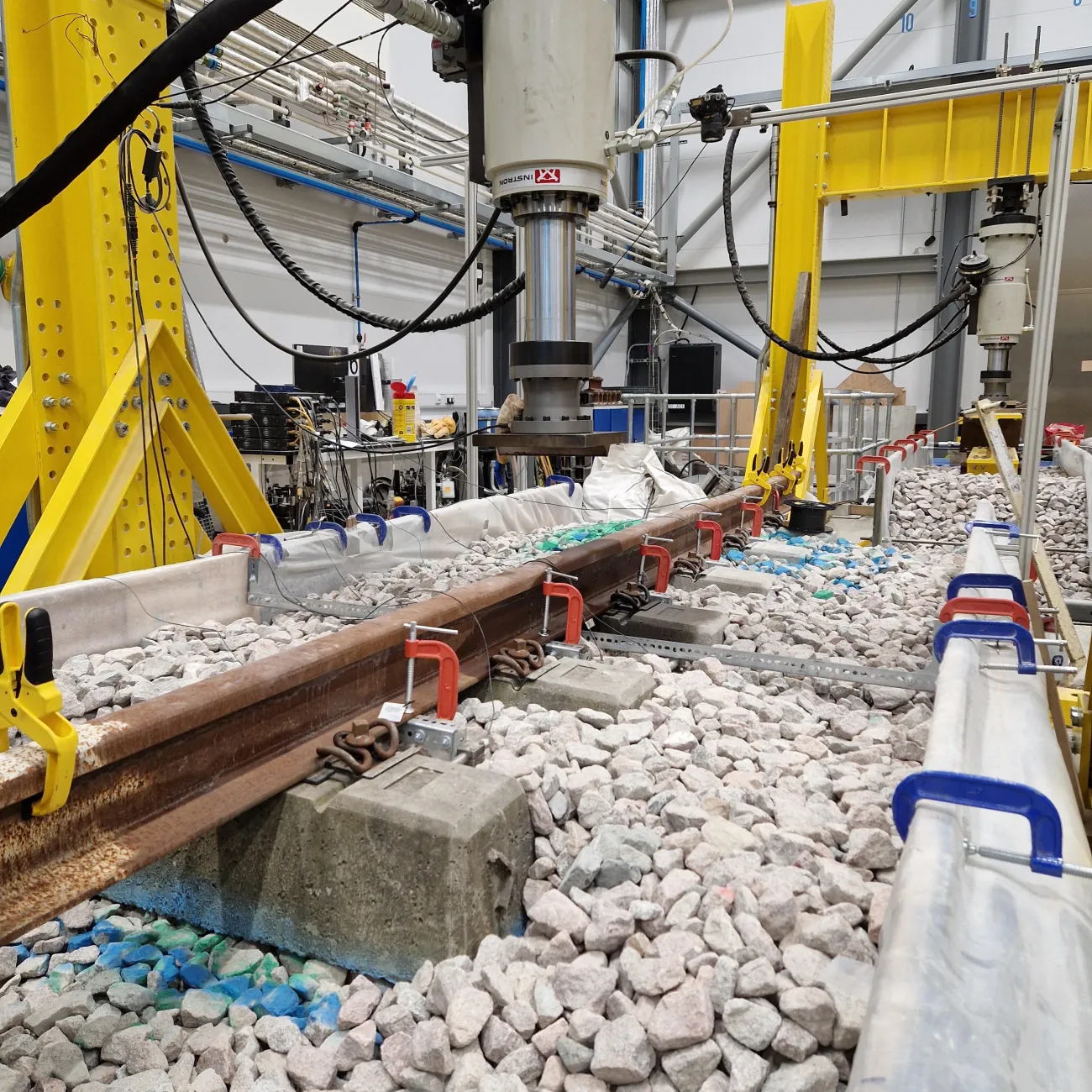
The research has overhauled how localised repairs are approached. David adds: “The driver was definitely cost – the fact that you’re not having to go back every six weeks when you’re monitoring it – but also cutting carbon.”
In the following years, these sensors were included in new rail lines and embedded during routine maintenance too. “We’ve built a system that’s got 60 sensors on a good piece of track to watch how it works from new,” David says. The research team was able to gather so much data it could ask important questions of it, including how much information was useful and at what point the data set became so large it no longer drove improvements.
Now the team is continuing its exploration of embedded monitoring sensors – including new fibre-optic sensors installed on track, here in the UK with Network Rail and working with European rail companies including SNCF in France.
This latest research is a collaboration with colleagues in our Optoelectronic Research Centre (ORC), where the special fibre-optic sensing systems are designed and made. These advanced sensors, called High-Resolution Distributed Acoustic Sensors (HR-DAS), can turn a single strand of fibre—thinner than a human hair—into thousands of tiny, highly sensitive sensors.
By attaching this fibre to a structure and connecting one end to a custom-built device (the "interrogator") developed by Dr Ali Masoudi and his team at the ORC, we can detect even the slightest vibrations and movements across the entire structure.
This breakthrough allows us to monitor large areas without needing thousands of separate sensors, making the process simpler, more efficient, and incredibly powerful. Ali and his team launched spin-out company SensiPhi (www.sensiphi.co.uk) to develop the sensors.
This technology has huge potential for changing the way rail networks are monitored, David says. “This research is really exciting because embedded fibre optics can be projected at scale: you could have a sensing fibre in the ground underneath the railway and, if you can put fibre in the trackbed, you could have a technology that measures performance along hundreds of kilometres.”